Plasma-SealTight® (PST)
Ultra-Strong and Media-Tight
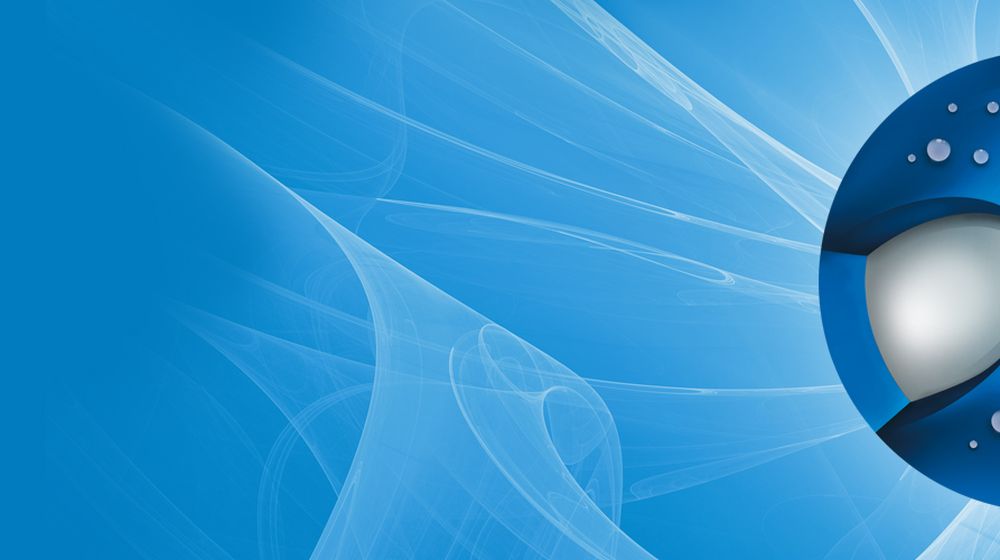
Plasma-SealTight®
The Extra Strong Hybrid Bond
Atmospheric Plasma Coating for Reliable Plastic-to-Metal Bonds in the Injection Moulding Process
Bonding thermoplastic compounds to metal is state-of-the-art in injection moulding and used in many industrial applications. However, the interface where the completely different materials meet is still regarded as a risk factor. If not properly sealed, it provides a permanent pathway for the ingress of water, air or other media in a plastic-to-metal bond.
Practical experience shows that even an injection-moulded bond that was originally tight can become untight over time, lose cohesion and ultimately lead to the functional failure of the components. In many cases premature adhesive failure is caused by the absorption of moisture in combination with oxygen, which results in subsurface migration at the interface. Water ingress in the boundary area leads to corrosion of the metal and in most cases to complete functional failure.
Image dimensions not found
Change image or reupload it
The turnkey PST plasma unit PTU1200
PST (Plasma-SealTight®) developed by Plasmatreat and AKRO-PLASTIC represents a completely new approach to obtaining a media-tight and very strongly bonded hybrid compound. This new industrial solution offers a process which precisely matches the composition of a plasma polymer layer generated under atmospheric pressure to the recipe for the plastic compound and the process parameters to create a long-time stable, media-tight bond of the injection-moulded part.
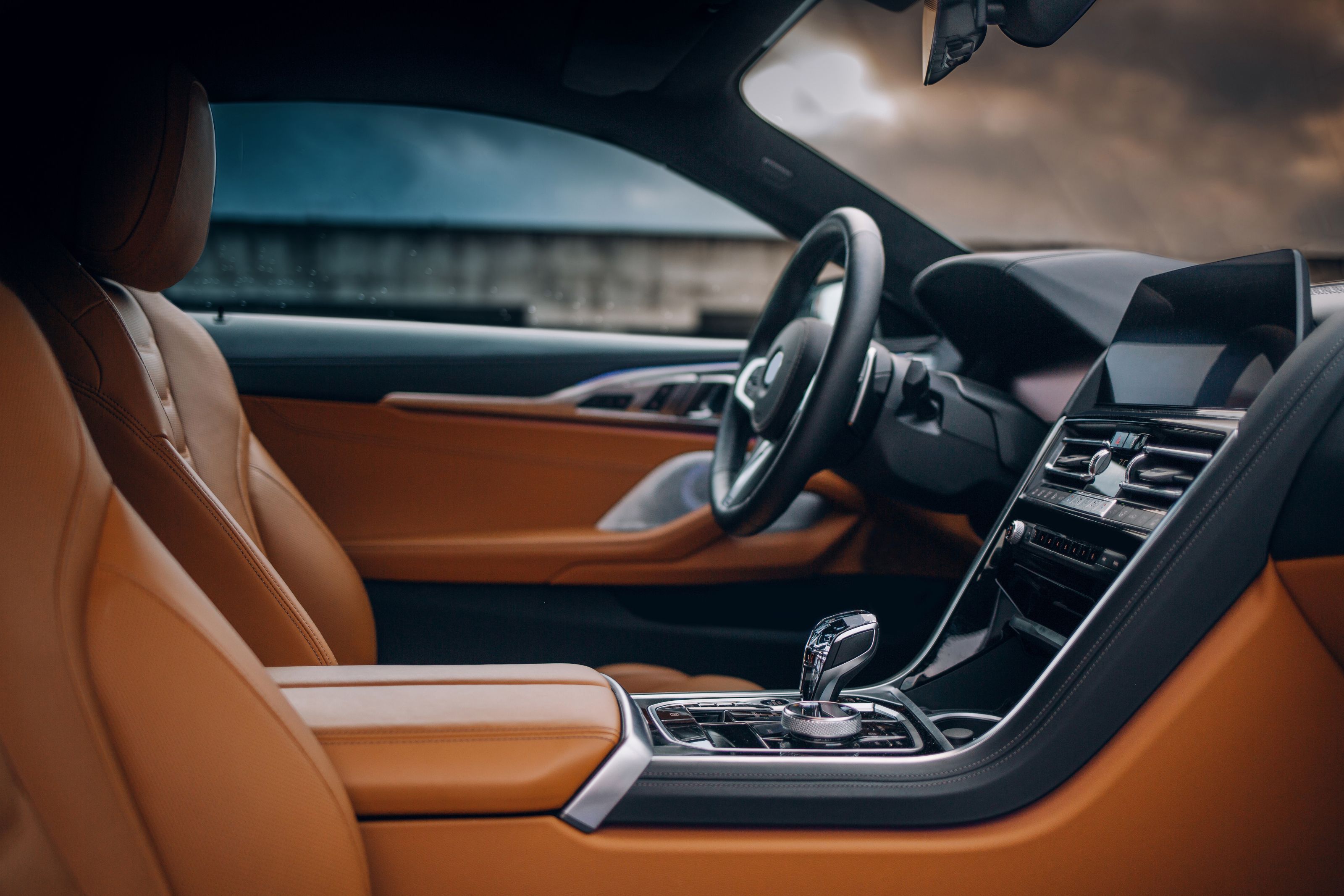
Plasma-SealTight®
Atmospheric Plasma Polymerisation
Plasmatreat and the Fraunhofer Institute for Manufacturing Technology and Advanced Materials IFAM, Bremen, developed Plasma-Plus® technology about ten years ago. Instead of using low pressure plasma produced in a special vacuum chamber, this technology enables thin film plasma coatings to material surfaces in-line under completely normal production conditions. The process is fast, robust and one hundred percent reproducible. Environmentally harmful processes, such as the use of solventbased primers can be entirely replaced without any ensuing loss of quality.
PlasmaPlus® is a chemical-physical process that creates a covalent bond between different materials by means of layer deposition in atmospheric pressure plasma. The layer bonds with the metal at molecular level and in combination with the adapted plastic compound it forms such a strong joint and tight seal that it takes on the function of an anticorrosive coating.
Image dimensions not found
Change image or reupload it
A special feature of the process is its great flexibility. In particular, the coating thickness and process speed can be precisely matched to a specific level of corrosion protection. Without doubt, the great advantage of this process over other coating techniques is the fact that layer deposition is area-selective, i.e. the nozzle technology enables it to be targeted with pinpoint accuracy to a precisely defined location, even at very high processing speeds. 100 nm thin coating, for instance, can be deposited in milliseconds, whereas it would take around one to two minutes to do this using low-pressure plasma and localized selection would not be an option.
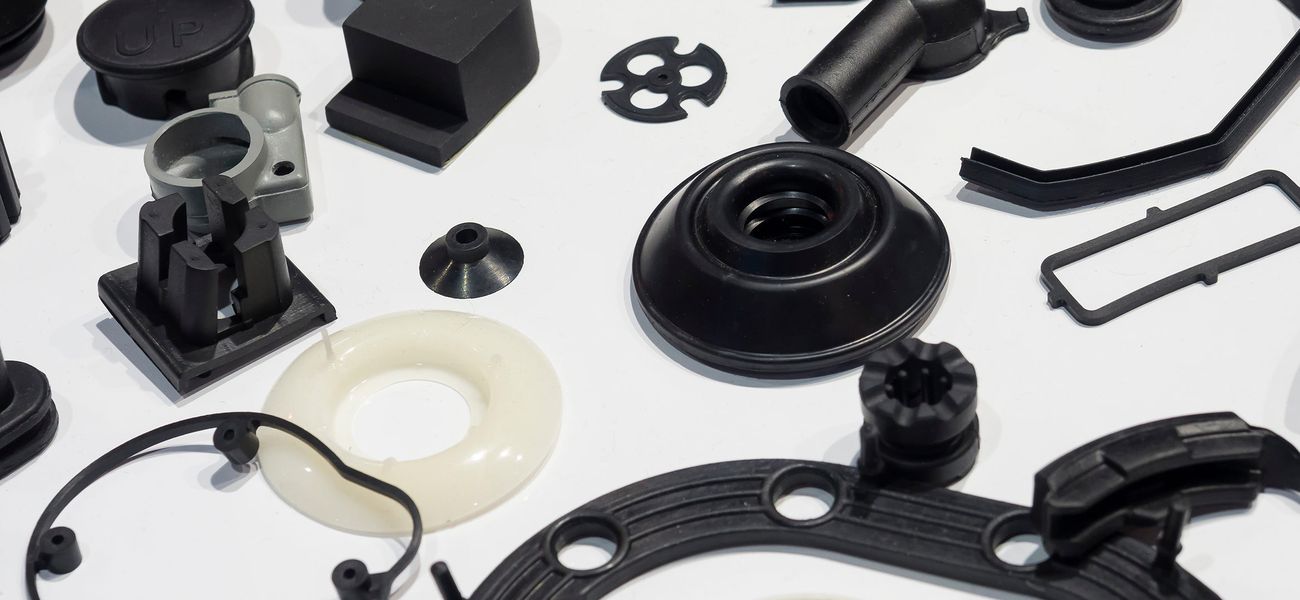
Find the Right Compound for Your Application
A selection of polyamides for your applications.
Produktreihe PST
PST Plastic Compounds
To guarantee consistent product quality and thus the functioning of subsequent components, the manufacturer must have an extremely precise and reproducible compounding process.
A specialist in customised adaptations of plastic compounds with a compounding technology developed in-house, AKRO-PLASTIC can ensure identical quality regardless of the production site. For the new technology the company created plastic compounds with specific properties which fulfil the requirements for functional integrity and quality.
Two main aspects had to be considered when developing the new chemical recipe: the different coefficients of linear expansion of plastic and metal on the one hand, and the chemical-physical adhesive bond with the plasma polymer layer on the other.
For the new process AKRO-PLASTIC has developed the PST product line, which includes the AKROMID® B3 GF 30 1 PST black (6647).
Also PBT thermoplastic polymer tests have shown good values. Testing is in its final stage.
Application
On the basis of the safety lock, Interlock AZM300, from the company K. A. Schmersal Holding GmbH & Co. KG, you can learn more about the advantages and solutions of the Plasma-SealTight® technology.
Plasma-SealTight® Technology
Tensile Test
Improved bond strength compared with adhesion promoters.
Plasma-SealTight® bonds to the metal (stainless steel, copper, aluminum, steel) at molecular level and at the same time generates organic compounds (functional groups) which ensure a strong adhesive bond between the metal and the plastic.
Tensile shear strengths of over 50 MPA can be achieved between plastic and metal with Plasma-SealTight®. Plasma coating achieves significantly higher bond strength than other processes such as adhesion promoters, laser micro-structuring or etching.
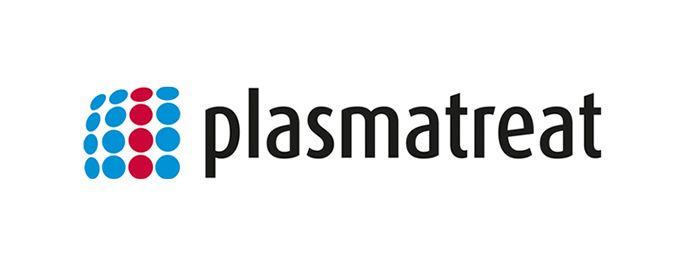
Plasma-SealTight®
Functional and Sustainable
The creation of a boundary layer between two dissimilar materials presents the developers with a major challenge, since the chemical properties of the layer call for the creation of a simultaneous bond between different materials. The task becomes even more complex if the materials belong to different groups, as is the case here with metal and plastic.
By developing new precursors and extensively adapting the plasma parameters, Plasmatreat succeeded in selectively incorporating several functions into a single layer with this new PST process. These functions include good bonding to the metal surface, enhanced corrosion resistance, acting as a media and oxidation barrier and adhesionpromoting properties for plastics through the creation of functional chemical groups. Silicon contained in the layer facilitates adhesion to metal and metal oxide, whilst silicon oxide is responsible for the barrier effect and media tightness. The organic components in the layer (functional groups) form the adhesive bond with the polymer.
Image dimensions not found
Change image or reupload it
Tensile test after PST-Verfahren
The new plasma coating developed for this process not only meets the above mentioned functional requirements; in addition its chemical composition and processing properties are reliable, non-hazard-ous, low-odour and environmentally friendly.
Plasma-SealTight®
Strongly Bonded and Media-Tight
Water can easily penetrate the boundary layer and spread across the surface of materials that do not have a chemically bonded connection. With the hybrid component described here, water in combination with oxygen would lead to corrosion of the metal, failure of the component function or even delamination. The PlasmaPlus® layer prevents this effect by filling in microscopic cavities like a fine mist, bonding to the metal surface and forming a corrosion-proof barrier.
PST (Plasma-SealTight®) ensures both strong adhesion and media-tightness of the material joint, and corrosion protection of the metal insert. The plasma polymerised covalent seal forms a longtime-stable barrier against water, salt solutions and gases and prevents the migration of these media.
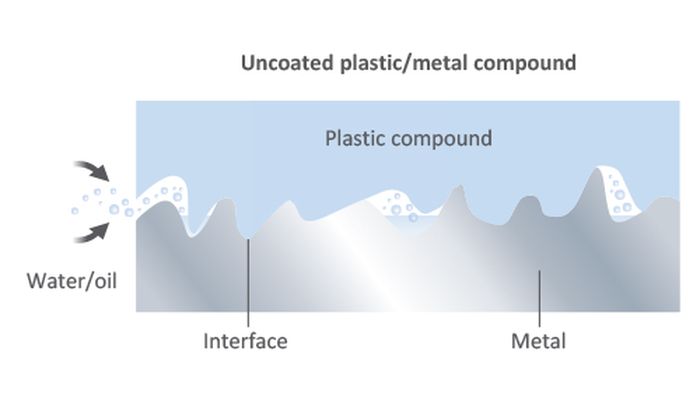
)
Plasma-SealTight®
High Reliability for Customers
This innovative coating process offers a pioneering solution for improving plastic-to-metal bonds in the injection moulding industry. The system partnership between the two specialists provides users with a particularly high degree of security for customised requirements. The new process also ensures greater product quality and a reliable, reproducible and cost-effective production process, whilst at the same time being completely environmentally benign.
Image dimensions not found
Change image or reupload it
PLASMATREAT GmbH
Manufactures Plasma Systems for Highly Effective Surface Treatments and Environmentally Friendly Production Processes
The Openair® plasma technology patented in 1995, from which the multi-award-winning Plasma-Plus® nanocoating process evolved, is now used in almost all sectors of industry. Close cooperation with leading research institutes and industry partners is a hallmark of the innovative spirit of the company. With technology centers in Germany (head office), the USA, Canada, Japan and China as well as subsidiaries and representatives in over 35 countries, the Plasmatreat Group ensures close proximity to its customers throughout the world.
Disclaimer: All specifications and information given in this brochure are based on our current knowledge and experience. A legally binding promise of certain characteristics or suitability for a concrete individual case cannot be derived from this information. The information supplied here is not intended to release processors and users from the responsibility of carrying out their own tests and inspections in each concrete individual case. AKROMID®, AKROLEN®, AKROLOY®, AKROTEK®, PRECITE®, AF-Carbon®, AF-Color®, AF-Complex®, AF-Clean, ICX®, BIO-FED®, M·VERA® and AF-Eco and are registered or applied trademarks of the Feddersen Group. Openair®-Plasma and PlasmaPlus® are registered trademarks of Plasmatreat GmbH. Copyright 2016. All text, images and photographs are copyrighted by Plasmatreat GmbH and AKRO-PLASTIC GmbH. All rights reserved.
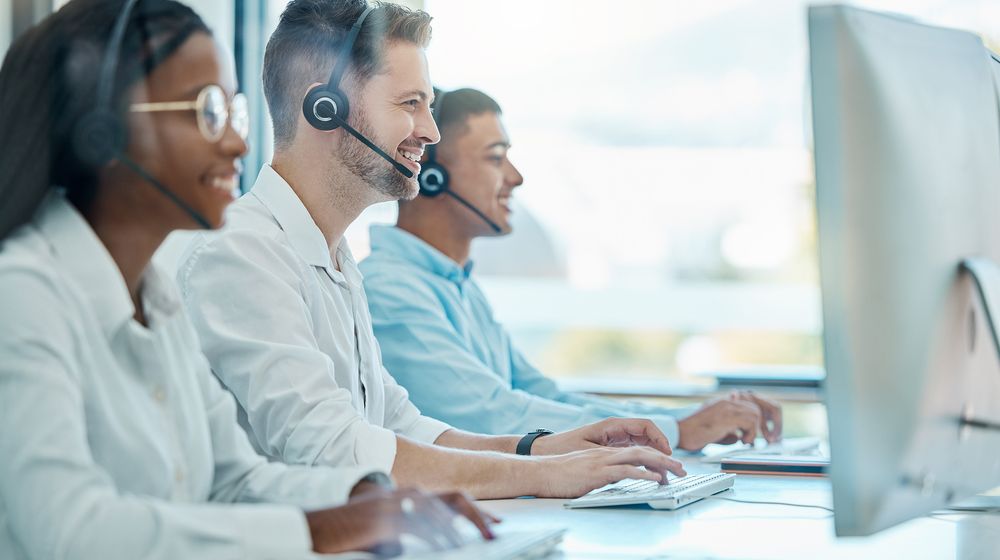