FLUID INJECTION TECHNIQUE
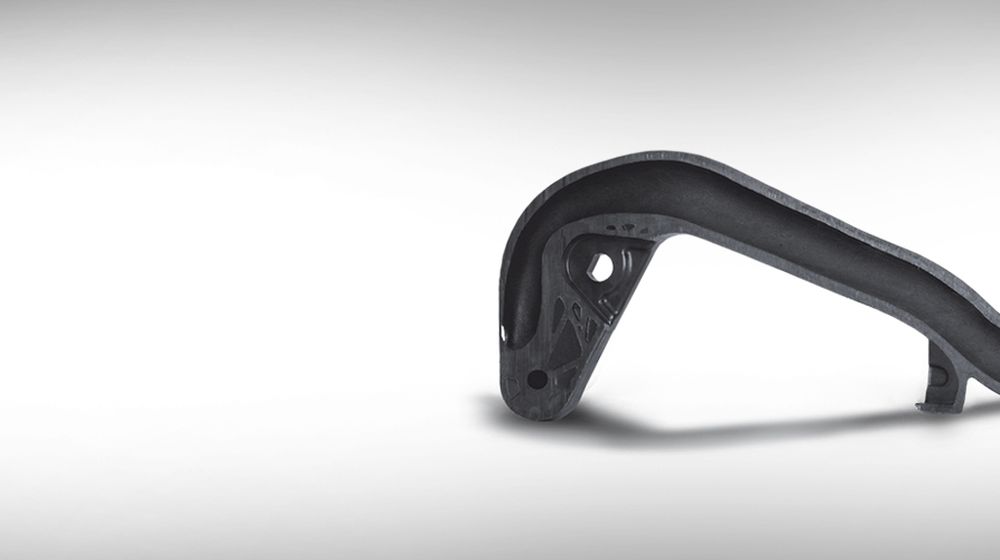
Fluid Injection Technology (FIT)
Fluid injection technology (FIT) is an overall term for special injection molding processes in which cavities are created by injecting a fluid into thick-walled, still flask-liquid component areas. Either gas (GIT) or water (WIT) can be used as the driving fluid. Projectile injection technology (PIT) is a process variant in which the melt is displaced by a rigid projectile which is driven through the component with the aid of a fluid (gas or water).
In FIT, the molding process is divided into two steps. First, the plastic melt is injected into the cavity in the same way as in conventional injection molding. Here, a frozen solidified edge layer forms on the mold wall while the melt core is still liquid. After a defined delay time, a fluid is injected into this molten core, which initially displaces the melt into unfilled (blow-out process) or additionally opened (secondary cavity process) cavities or back into the screw cavity (melt back pressure process). The fluid thus forms a cavity.
Fluid injection technology can be used to produce functional cavities such as media lines, as well as long and very thick-walled components such as handles, for which very long cooling times would otherwise be necessary and there can be increased problems with sink marks. Particularly with the mass-reversing and short-shot processes, component weight can be reduced by up to 60 %, thus cutting both material costs and CO2-emissions. In vehicles, this also means significant CO2-savings in the use phase. Compared with foam injection molding, where a weight reduction can also be achieved through the processing procedure, the surfaces of FIT components are generally better.
Gas Injection Technique & Water Injection Technique
Suitable Materials
The following materials from AKRO-PLASTIC are suitable for the gas and water injection technique, depending on the application:
Handles:
AKROMID® A3 GF 30 1 GIT black (4619) = good surface finish, safe process
AKROMID® A3 GF 15 1 GIT black (4620) = good surface finish, safe process
AKROMID® B28 GF 50 1 GIT black (4732) = good surface finish, safe process
AKROMID® B3 GF 30 1 GIT black (4598) = good surface finish, safe process
AKROMID® B3 GF 30 1 GIT black (4599) = extremely good surface finish
Cooling water pipes:
AKROMID® A3 GM 20/10 4 WIT black (4529) = thin walls, safe process
Process Variants
Image dimensions not found
Change image or reupload it
Melt Pushback
The component is completely filled and the melt is then forced back into the screw unit by means of fluid or a projectile.
Image dimensions not found
Change image or reupload it
Overflow Cavity
The component is completely filled and the melt is then forced into a secondary cavity by means of fluid or a projectile.
Image dimensions not found
Change image or reupload it
Short Shot
Inflation method:
The component is partially filled (generally 60-90 %) and the melt is then inflated with fluid by means of an injector close to the sprue.
If the melt is displaced with a projectile as well as with the fluid, the process is called projectile injection technology (PIT). This can be combined with various filling methods as well as different fluids.
Talk to Our Experts
With a worldwide network of plastics distribution experts, we can provide you with support anywhere in the world. Talk to one of our specialists to find out more.
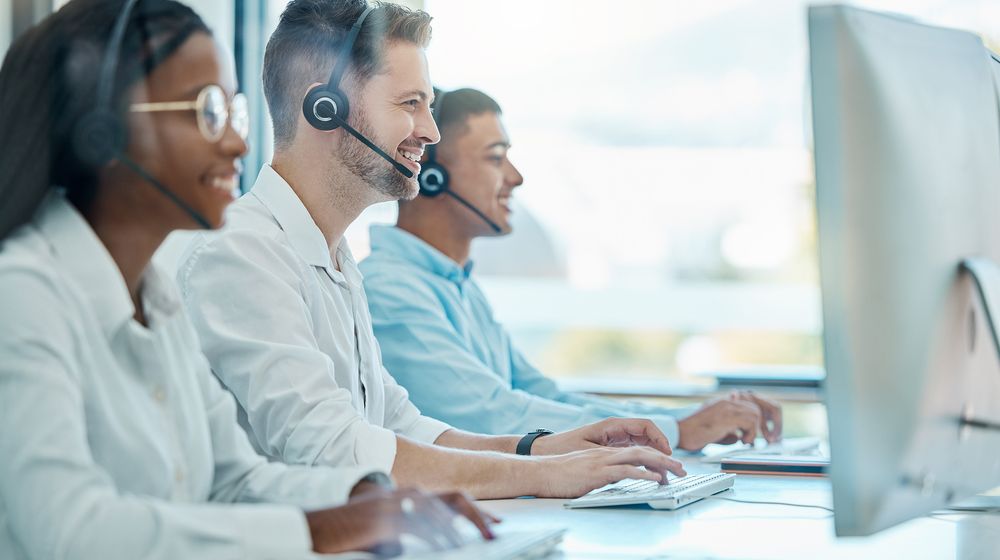