Corona-Shield holder
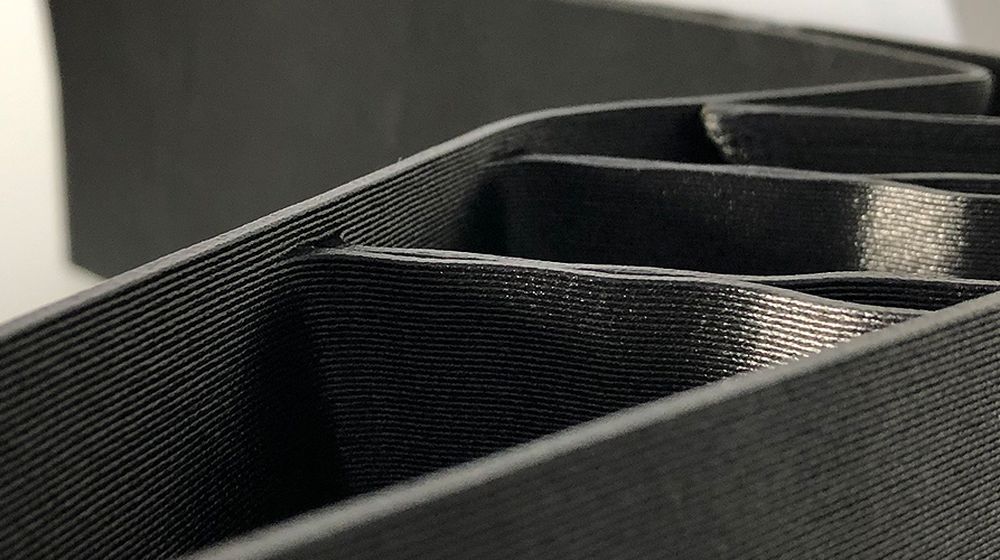
Image dimensions not found
Change image or reupload it
Successful implementation of a project with pellet 3D printing: a breakthrough for cost-efficient production
Vehicle manufacturer: Volkswagen
Raw material manufacturer: AKRO-PLASTIC GmbH
Machine manufacturer: Yizumi Germany GmbH
Parts manufacturer: Faurecia Autositze GmbH
In an impressively short period of time, YIZUMI, in collaboration with Faurecia and AKRO-PLASTIC, has implemented an innovative project that demonstrates the advantages of pellet 3D printing. It only took around four months from the initial idea to delivery of the final part. During this time, three validation runs with front and rear crashes at 50 km/h were successfully completed.
More information about 3D-Printing: Klick here
Fast and efficient production
Fast implementation: The entire order was realized from idea to delivery in just four months, including three validation runs with crash tests at 50 km/h.
Cost-efficient production: A large-volume structural component measuring 600 mm x 300 mm x 200 mm and weighing around 810 g was produced for less than €13.50/pc in a batch size of 750 parts and delivered to Faurecia. This was the first time that an AM technology was used to achieve a material cost share of almost 50% in a plastic component using a market-proven injection molding grade.
Continuous operation: Production took place over five weeks in 24/7 operation, including the Christmas vacations. This was made possible by integrating a conveyor belt into an AM cell, which meant that no manual interaction was required.
Design: The design of the component was load-path and production-oriented.
Innovative approach: YIZUMI's special approach in cooperation with AKRO-PLASTIC was to achieve significant cost benefits through additive manufacturing (AM) production with minimal changes to standard designs. The materials from AKRO-PLASTIC could be processed extremely effectively. YIZUMI built the systems at minimal cost, which meant that system-related problems could be solved quickly and cost-effectively.