3D Printing
Additive manufacturing for series production
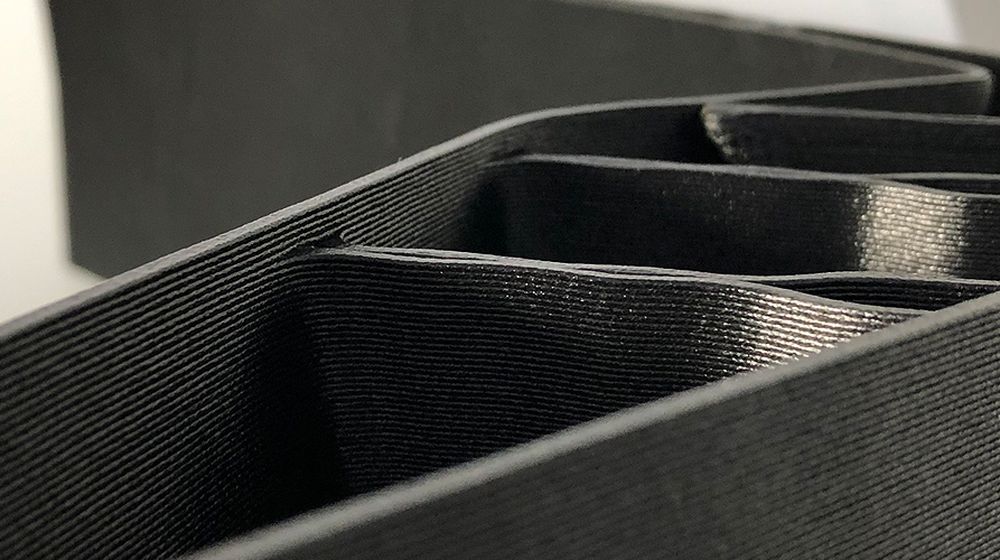
Additive Manufacturing Becomes 30 Times Faster
Performance and Productivity in 3D Printing
Large-format parts, high volumes, maximum productivity - 3D printing with granules opens up new application areas for additive manufacturing. 3D printing is becoming a well-established manufacturing process in a growing number of industry sectors, including the automotive, transportation and renewable energy sectors. Directly processing thermoplastic pellets using screw extrusion in additive manufacturing enables high production speeds of up to 400 mm/s, high output rates > 2 kg/h and build volumes in the cubic meter range.
Image dimensions not found
Change image or reupload it
Overview of manufacturing processes
Additive or generative manufacturing methods are defined as processes in which components are built up layer by layer starting from 3D volume models. Unlike injection molding, no tool is required. These processes are often also referred to as 3D printing and include several technologies that differ in the materials used and the process of generative built-up. For example, sintering processes with powders (powder bed fusion), photopolymerization of liquid polymers and material extrusion are used to process plastics. Material strands are deposited in extrusion processes (FLM - Fused Layer Modeling). Plastics are fed in extrusion processes as filament (FFF - Fused Filament Fabrication) or in the form of pellets (FGF - Fused Granulate Fabrication).
In subtractive manufacturing, on the other hand, a component is produced by removing material. For example, a smaller component is created from a material blank by grinding, drilling or milling.
Parts produced by 3D printing are often post-processed to achieve improved dimensional and surface tolerances. Particularly in the FGF process also called SEAM (Screw Extrusion Additive Manufacturing), the combination of additive and subtractive manufacturing is useful to additively print components with a high output rate and to locally rework functional areas by subtractive processes.
Show more
Advantages of FGF
Why pellet printing revolutionizes additive maufacturing
Machine and part sizes in pellet printing
Facts about pellet printing
General
AKRO Compounds
Material qualification at AKRO-PLASTIC
Applications
Realized projects in large format 3D printing with pellets
Disclaimer: All specifications and information given on this website are based on our current knowledge and experience. A legally binding promise of certain characteristics or suitability for a concrete individual case cannot be derived from this information. The information supplied here is not intended to release processors and users from the responsibility of carrying out their own tests and inspections in each concrete individual case. AKRO®, AKROMID®, AKROLEN®, AKROLOY®, AKROTEK®, ICX®, PRECITE® and DIA(hr)LOG® are registered trademarks of AKRO-PLASTIC GmbH.