Mittelkonsolenträger
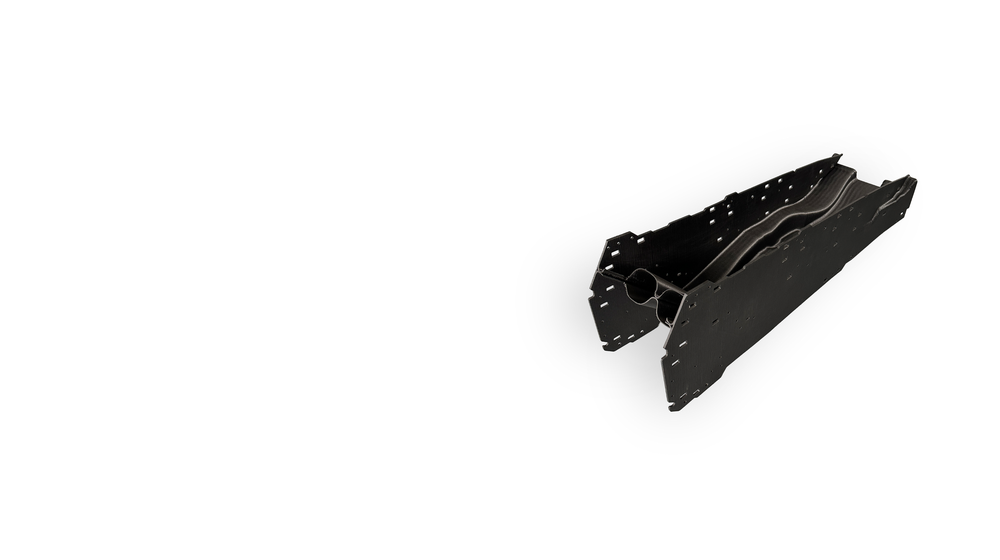
SPE Award 2024 - Kategorie "Grand Award"
Mittelkonsolenträger-Produktion
Fahrzeughersteller: BMW AG
Rohstoffhersteller: AKRO-PLASTIC GmbH
Maschinenhersteller: Hans Weber Maschinenfabrik GmbH
Teilehersteller: BMW AG
Die Herstellung des Mittelkonsolenträgers, einer kritischen Komponente im Automobilbau, hat eine beeindruckende Transformation erfahren. Mit einer Produktionsmenge von etwa 8000 Einheiten pro Jahr und einem Gewicht von rund 10 kg pro Einheit wird erstmals ein additives Herstellungsverfahren eingesetzt. Dieses innovative Verfahren, bekannt als Large Scale Printing (LSP), kombiniert robotergestütztes Drucken mit nachgeschalteter mechanischer Endbearbeitung und markiert einen bedeutenden Fortschritt in der Fertigungstechnologie.
Das LSP Verfahren zeichnet sich durch eine deutlich erhöhte Wirtschaftlichkeit aus. Die wesentlichen Faktoren dabei sind der Einsatz von Granulat als Ausgangswerkstoff, die hohe Austragsleistung des Endeffektors und die niedrigen Investitionskosten für ein Anlagensetup.
Hochleistungsmaterialien und Prozessstabilität
Ein weiterer Vorteil des LSP-Verfahrens ist der Einsatz von hochgefülltem, faserverstärktem Spritzgussgranulat. Dieses Material bietet nicht nur hervorragende mechanische Eigenschaften (E-Modul >14 GPa, Bruchspannung >160 MPa, Bruchdehnung >3,5 %), sondern auch eine ausgezeichnete Prozessierbarkeit und geringen Verzug bei der Bauteilherstellung. Diese Eigenschaften garantieren eine hohe Qualität und Beständigkeit der produzierten Bauteile.
Image dimensions not found
Change image or reupload it
Wirtschaftlichkeit und Effizienz des LSP-Verfahrens
Das LSP-Verfahren zeichnet sich durch eine außergewöhnliche Wirtschaftlichkeit aus.
Einsatz von Granulat als Ausgangswerkstoff, was die Materialkosten erheblich senkt.
Hohe Austragsleistung des Endeffektors, der mehr als 1 kg/h verarbeitet, ermöglicht eine schnelle und effiziente Produktion.
Niedrige Investitionskosten für das Anlagensetup, was die Einstiegshürde für die Implementierung dieser Technologie verringert.
Designoptimierung und Funktionsintegration
Durch ein intelligentes Bauteildesign konnte der Mittelkonsolenträger im Vergleich zur bisherigen differentiellen Hybrid-Bauweise (Metall/Kunststoff), mittels Funktionsintegration optimiert werden. Die Teiligkeit konnte von 7 auf 1 Bauteil reduziert werden. Neben dem Entfall von zusätzlichen Ur- und Umformwerkzeugen kann die Werkschöpfungskette (z. B. Montage) deutlich verkürzt werden.
Durch Simulation und Hardwareversuche konnten alle relevanten funktionalen Anforderungen bestätigt werden (KWT- Shaker, Eigenfrequenz/Modalanalyse, Festigkeits- u. Steifigkeitsnachweis, Crashsimulation). Das eingesetzte Verfahren ermöglicht es erstmals ein Serienprojekt der vorliegenden Bauteil- und Losgröße in additiver Fertigung umzusetzen.
Image dimensions not found
Change image or reupload it
Nachhaltigkeit durch Materialsubstitution und Effizienzsteigerung
Gegenüber der vorherigen Aluminiumhybrid-Bauweise des Mittelkonsolenträgers kann ein wesentlicher Beitrag zur Nachhaltigkeit des Fahrzeugs erzielt werden. Durch die Implementierung des neuen Verfahrens und Materials können pro Einheit ca. 84 kg CO2 pro Fahrzeug eingespart werden.
Der eingesetzte Werkstoff (PA 11 ICF 40) zeichnet sich durch einen CO2-Fußabdruck von nur 1,6 kg CO2/kg aus: AKROMID® NEXT U28 ICF 40 1 schwarz (8238)
Das verwendete Polymer PA11 ist biobasiert und wird aus Samen der Rizinuspflanze gewonnen. Der Anbau steht nicht in Konkurrenz zur Nahrungsmittelproduktion.
Durch den Einsatz einer PIR-Kohlenstofffaser als Verstärkung wird der CO2 Footprint des Compounds effektiv reduziert.